Quick and Reliable Packaging Machine Fixing Provider to Reduce Downtime
In the competitive landscape of production, the effectiveness of packaging procedures rests on the reliability of equipment. Quick and trustworthy repair work services are crucial in reducing downtime, which can lead to substantial operational obstacles and financial losses. Recognizing the significance of prompt interventions and the duty of professional technicians can change how services approach maintenance and fixings. Nevertheless, browsing the myriad choices readily available for repair work solutions can be challenging. What variables should companies take into consideration to ensure they are making the ideal selection for their operational requirements?
Importance of Timely Services
Timely repairs of packaging equipments are crucial for keeping functional efficiency and decreasing downtime. In the hectic setting of manufacturing and packaging, even minor breakdowns can lead to substantial hold-ups and productivity losses. Resolving issues promptly makes sure that equipments operate at their optimal capability, therefore guarding the flow of procedures.
Moreover, prompt and regular upkeep can prevent the escalation of small problems into major break downs, which typically incur greater fixing expenses and longer downtimes. A proactive approach to equipment repair service not only maintains the honesty of the devices but additionally improves the total dependability of the production line.
In addition, prompt repairs add to the durability of product packaging machinery. Machines that are serviced without delay are less most likely to experience from excessive deterioration, allowing services to maximize their financial investments. This is especially vital in industries where high-speed product packaging is important, as the demand for constant efficiency is critical.
Advantages of Reliable Provider
Reputable solution providers play a pivotal role in guaranteeing the smooth operation of packaging makers. Their experience not just boosts the performance of repairs but also adds significantly to the longevity of tools.

In addition, a reputable company offers comprehensive support, consisting of training and guidance for team on machine procedure and upkeep finest methods. This not only equips employees but also grows a society of security and effectiveness within the organization. In general, the benefits of engaging dependable service providers expand past instant repair work, positively impacting the whole functional workflow of packaging procedures.
Typical Packaging Machine Concerns
In the world of packaging procedures, numerous problems can compromise the performance and capability of devices. One prevalent trouble is mechanical failing, often originating from damage or insufficient maintenance. Elements such as motors, belts, and equipments might fail, bring about malfunctions that halt manufacturing. Another usual issue is imbalance, which can cause jams and unequal packaging, affecting product high quality and throughput.
Electric problems can likewise disrupt packaging procedures. Faulty electrical wiring or malfunctioning sensing units might result in unpredictable equipment habits, creating delays and boosted operational expenses. In addition, software glitches imp source can impede the equipment's programming, causing functional inefficiencies.
Inconsistent product circulation is an additional essential problem. This can occur from variations in product size, shape, or weight, which might influence the maker's ability to deal with products precisely. Not enough training of drivers can aggravate these troubles, as inexperienced employees might not identify very early signs of malfunction or may abuse the tools.
Addressing these common packaging machine issues promptly is vital to maintaining productivity and ensuring a smooth procedure. Normal assessments and positive maintenance see this website can considerably mitigate these concerns, cultivating a trusted product packaging atmosphere.
Tips for Lessening Downtime
To reduce downtime in packaging procedures, carrying out a positive maintenance approach is vital. On a regular basis arranged maintenance checks can recognize prospective issues prior to they intensify, making sure makers operate successfully. Developing a routine that consists of lubrication, calibration, and evaluation of critical parts can considerably reduce the regularity of unexpected malfunctions.
Training team to operate equipment properly and identify early caution signs of breakdown can also play a crucial role. Encouraging operators with the understanding to perform fundamental troubleshooting can prevent minor concerns from causing significant hold-ups. Furthermore, keeping a well-organized stock of important extra parts can quicken repair work, as awaiting components can result in extensive downtime.
In addition, recording machine performance and maintenance activities can aid recognize patterns and persistent troubles, enabling targeted interventions. Integrating sophisticated surveillance modern technologies can provide real-time data, allowing predictive upkeep and lessening the threat of abrupt failings.
Last but not least, fostering open communication between operators and maintenance teams ensures that any irregularities are quickly reported and dealt with. By taking these positive procedures, services can improve operational effectiveness and substantially minimize downtime in packaging processes.
Choosing the Right Repair Work Service
Selecting the appropriate fixing solution for product packaging makers is an essential choice that can substantially affect operational efficiency. An appropriate solution supplier guarantees that your machinery is fixed Visit This Link promptly, successfully, and to the highest standards. Begin by reviewing the copyright's experience with your details kind of packaging tools. A professional acquainted with your machinery can detect problems much more properly and carry out services more swiftly.
Next, take into consideration the service copyright's credibility. Looking for feedback from various other businesses within your market can supply insights into dependability and top quality. Qualifications and partnerships with identified equipment makers can also suggest a dedication to excellence.
Furthermore, assess their reaction time and schedule. A company that can offer timely assistance decreases downtime and keeps production circulation steady. It's likewise critical to ask about service warranty and solution guarantees, which can show the self-confidence the copyright has in their work.

Conclusion
To conclude, the value of fast and dependable packaging machine repair service services can not be overemphasized, as they play a vital role in decreasing downtime and guaranteeing operational effectiveness. By prioritizing prompt repairs and picking reliable solution companies, organizations can efficiently keep and deal with usual issues efficiency. Implementing positive upkeep practices and purchasing team training further boosts the longevity of packaging equipment. Ultimately, a tactical strategy to repair services promotes a more durable manufacturing setting.
Timely repair services of product packaging equipments are crucial for maintaining operational efficiency and reducing downtime.Furthermore, timely repair work contribute to the durability of packaging machinery. In general, the benefits of engaging dependable service providers extend beyond prompt fixings, favorably influencing the whole functional operations of packaging processes.
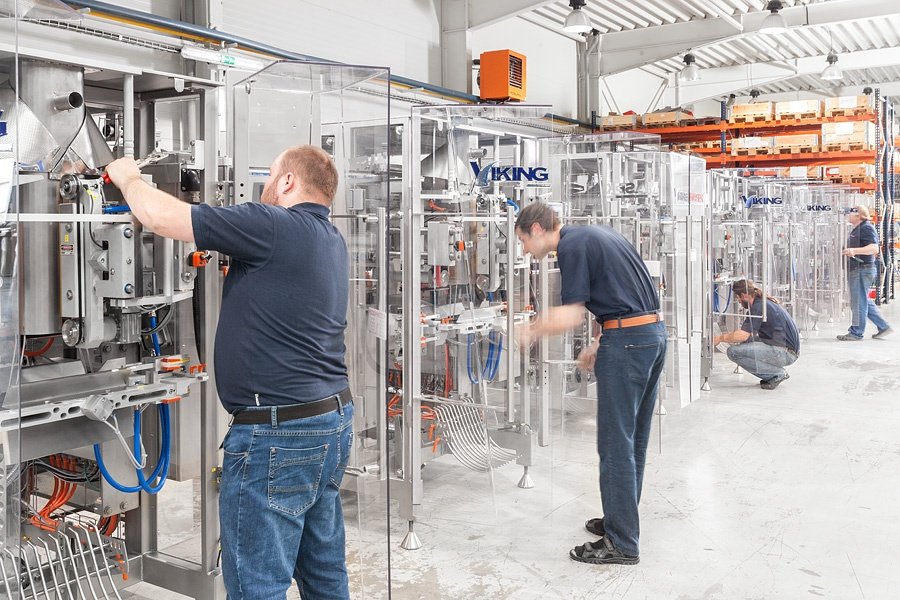